In late November of 2022, House of Horvath conducted a virtual cigar tasting and Q&A session with legendary cigar maker Manuel “Manolo” Quesada and his daughter Raquel
A select group of tobacconists from across Canada were invited to the event, and were treated to a special evening of conversation with the Quesada pair. Participants were also afforded the pleasure of smoking two new Casa Magna releases: the Connecticut and the Liga F, while a roller and buncher from the Quesada factory assembled cigars before everyone’s eyes.
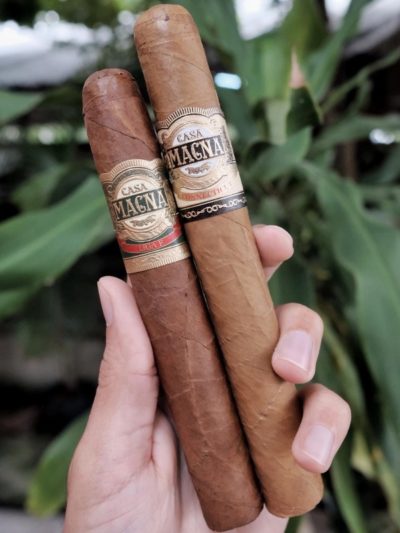
Left to right: Casa Magna Liga F and Connecticut
As expected, a wealth of cigar knowledge and history was shared by Manolo and daughter Raquel.
The following are excerpts of conversation between House Horvath Brand Ambassador Kurt Bradley and Manolo and Raquel Quesada, and is part 1 of a 2 part series.
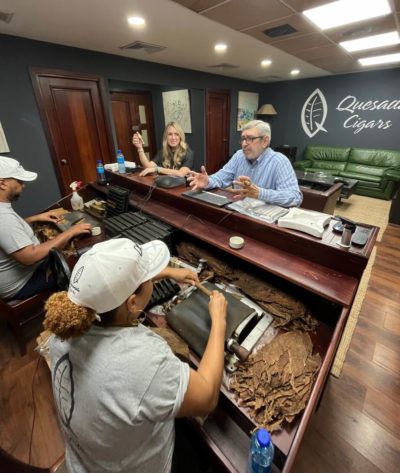
Manolo and Raquel answer questions as a roller and buncher work away
Kurt Bradley: Let’s discuss your new Casa Magna Connecticut. What are your feelings about Connecticut wrapper leaf, and how did this cigar come to be?
Manolo Quesada: I have always favored the Connecticut wrapper, and even more so after they started growing them in Ecuador. The Connecticut is a great blending wrapper, and it brings a little more enthusiasm to blends, as well as a creaminess. It is not as difficult to blend as the Connecticut from the valley in the United States. That Connecticut needs a little more care than the Connecticut from Ecuador.
Even though it’s a light-colored wrapper, it will fool you as it is not a light cigar. It definitely has personality to it, a little intensity. Enough intensity to allow the flavors to come through so you can enjoy the cigar.
Kurt: So it’s a pretty strong cigar then?
Manolo: Today they translate the word “intensity” into “strength”. I don’t like the word strength; I like the word intensity better. In cigar making, if we concentrate too much on a lot of intensity, we do not allow the palate to enjoy what the blend can bring because the other tobaccos are not showing up. We must blend so that the intensity is on a level that allows all the tobacco to play on the palate which lets the smoker enjoy all the nuances that the blend can offer.
So with the Connecticut the idea was to make a cigar in the Casa Magna style, but with a little creaminess that the wrapper brings to the blend. I have to say that I am very pleased with the blend that came out of it. I’ve been making Connecticut cigars for over 48 years now, and this one stands out with an intensity level that is a bit unusual for a Connecticut-wrapped cigar.
Raquel Quesada: It’s definitely not your typical Connecticut.
Kurt: Of course, the Connecticut is one of two new cigars that we’ll be smoking here, the other one being the Liga F. What does the ‘F’ in Liga F stand for?
Raquel: The F stands for “fuerte”, which in English means “strong”. We blended this cigar along the Casa Magna Colorado profile, but with Nicaraguan and Dominican tobaccos. The Colorado is a Nicaraguan puro. In having both Nicaraguan and Dominican tobacco in the Liga, it delivers a lot of flavor, but will still be on the stronger side. That’s the profile that we wanted to get out of the Liga F.
Manolo: The Casa Magna F is the first Casa Magna made in the Dominican Republic, and since we were making it in the Dominican Republic we felt that we had to blend Nicaraguan tobacco with some of our Dominican tobaccos as well. So, the blend has Dominican fillers and a Dominican binder, all grown from Cuban seed. The wrapper is a corojo, again from Ecuador which is a lovely wrapper. The cigar has a great blend to make the cigar a little more intense as well.
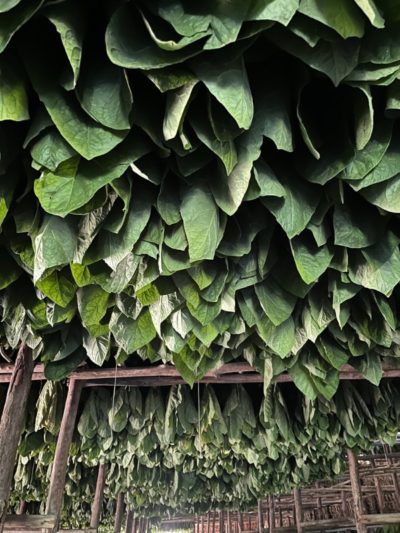
Tobacco cures to be blended in Quesada cigars
Again, speaking of intensity, I am not into things that fight with me. With cigars, I need them to be my companion. My philosophy in making cigars is to make them intense, but only intense enough so that you can enjoy the whole experience. We have to find a very delicate balance where you have a level of intensity that will allow you to enjoy the rest of the nuances that the blend will give you on the palate.
Kurt: Raquel, you represent the fifth generation of Quesadas to work in the tobacco business. It seems that from the get-go, you dove right into tweaking some of your father’s cigars to even blending some of your own. What can you tell us about your childhood growing up around tobacco, up to what has ultimately become your position as one of the most prominent roles within the company?
Raquel: I have many fond memories of my childhood growing up in a tobacco family business. When we were very young, my sister, my cousins and I would be running around all of the bales – even at times with my father and my grandfather. That tobacco aroma brings me back to when I started, around the year 2000. My father always said that we have to understand every stage of the process so that when we ultimately occupy a position at the top, we will understand what people are doing at every level of the company – top to bottom.
So I did every single process. I made cigars, I did tobacco stripping, I classified the cigars by color before they go in the boxes, a process that I hated at first, but have grown to appreciate and has become second nature to me.
Kurt: Raquel, on your social media videos I notice that you cut your cigar and then typically smell the tobacco aroma through the freshly cut cap prior to lighting. Can you expand on this routine cigar ritual of yours?
Raquel: I want to see how the fermentation process and the marriage of the tobacco turned out. It’s a romanticism that the tobacco industry gives you. The cigars talk to you and tell you how it’s going to be, what it will taste like.
Monolo: Dry smoking a cigar before you light it is a good idea because it gives you a pretty clear picture of what’s coming when you light the cigar. If you draw dry, you will start to get all of the nuances that will come to the palate when you light the cigar. I do that. Then I compare how the dry smoke was in comparison to the lit smoke.
Kurt: What does a normal day at Quesada look like for each of you?
Raquel: When I’m not travelling [laughs], we come in very early, which is something I learned from my father. Getting in early and staying there for the full day until 5 pm. It depends on the day. Sometimes we have cigar panels to try different things, or address projects that are underway or are about to begin. We often smoke and taste the different tobaccos before we start blending. I go to production, we look at US sales, international sales – there’s a lot going on. Sometimes we need extra hours.
Manolo: Smoking a cigar is a surreal experience and walking into our cigar factory is the same thing for me. First thing you do is listen to hear that the chavetas are hitting the table, which means they [the factory workers] are working and not being lazy. Then you start looking, touching, and tasting the tobacco. It’s a sensorial experience from the moment you walk into the factory up until the moment you go home.
Later, you carry all those experiences home with you so when you smoke a cigar at home, you’re remembering the all different senses that you experienced when you walked through the cigar factory earlier that day. This is really the beauty of the cigar factory and smoking, where all the senses are at play and are being experienced and enjoyed individually and jointly.
“Contrary to wine, where every year is different – and consumers allow for that difference – in our cigar world, we are expected to make the same cigar to infinity.” – Manolo Quesada
Kurt: Could you give us some back story on the history of this world-renown cigar family you hail from?
Manolo: It all started with my great grandfather in 1876 in Cuba. In Cuba we were not cigar makers – we were ‘leaf brokers’. We didn’t become cigar makers until after exile to the Dominican Republic. In Cuba we would buy tobacco, to sort, ferment and sell as raw materials the world over. We left Cuba in 1961 after we “donated” everything we had to the new government and then we came to the Dominican Republic to initially start again as leaf brokers. In 1974 the family decided that we should start a cigar factory, and in that raffle, I got the winning ticket. I was sent to the Free Zone (Zona Franca) to start a cigar factory with just $100, a table, a chair, a telephone and 3 cigar makers. 48 years later, here we are, still making cigars – only with a little more than a table, a chair and 3 cigar makers [laughs].
Kurt: At one point you were given the responsibility of making cigar brands that were once exclusively Cuban, but now had both a Cuban and a separate international rights holder, post-Cuban revolution. Brands like Romeo Y Julieta and Fonseca for example. Being a Cuban exile, how did it feel to manufacture and serve as a steward to such brands?
Manolo: It was a huge challenge, as you were looking at names that had a lot of pressings in the market. You couldn’t risk making the wrong cigar for either Fonseca or Romeo y Julietta; you had to make cigars that paid honor to those names. Thankfully we made Romeo y Julietta for 25 years and Fonseca for 44 years – so I guess we did something right.
Kurt: Cigar making certainly sounds like it comes with a great deal of responsibility and pressure.
Manolo: Making cigars is always a lot of pressure. At work, the only the only thing we can think about is the cigar. All a worker can think about is what goes on in their square meter of space. If they don’t, and their mind gets distracted, then the cigars are not going to perform the way that they should perform. It behooves us to be very on top of them [the factory workers] all day long; touching, smoking, opening cigars, draw mastering, and other things to ensure that every single one of them will perform the way they should perform, both mechanically – in that they will burn properly, draw properly and the wrappers are placed right – but also blend-wise, as the blend has to be exact in each individual cigar.
Contrary to wine, where every year is different – and consumers allow for that difference – in our cigar world, we are expected to make the same cigar to infinity. It becomes a more difficult proposition because tobacco crops are not infinite, tobacco crops end. You use one crop, and you have to substitute it with another crop. This is what we call the overlap; to maintain the integrity of the blend through time.
There is a greater degree of difficulty to make something that in 45, 50, 60 – 80 years will remind the consumer that he is essentially smoking the same cigar that he did 40 years ago. They are not exactly the same cigar, but differences in the profile and the blend will be so small, that he will not notice the difference if the integrity of the profile is properly maintained.
This is the peak of the art of making cigars. If this can’t be done properly, then you start making cigars that are all over the place and the customer will eventually call you and say, “what in the hell are you doing down there?”
[This concludes Part 1 of a 2 part series. Read Part 2 of the Quesada interview HERE]